In the heart of Italy’s furniture-making region, master artisans at prestigious workshops like Modenese Bespoke continue a centuries-old tradition of creating extraordinary pieces that blend timeless beauty with unparalleled craftsmanship. These craftspeople, working in small workshops scattered throughout regions like Veneto and Lombardy, represent the pinnacle of furniture making, where each piece tells a story of dedication, skill, and artistic vision passed down through generations.
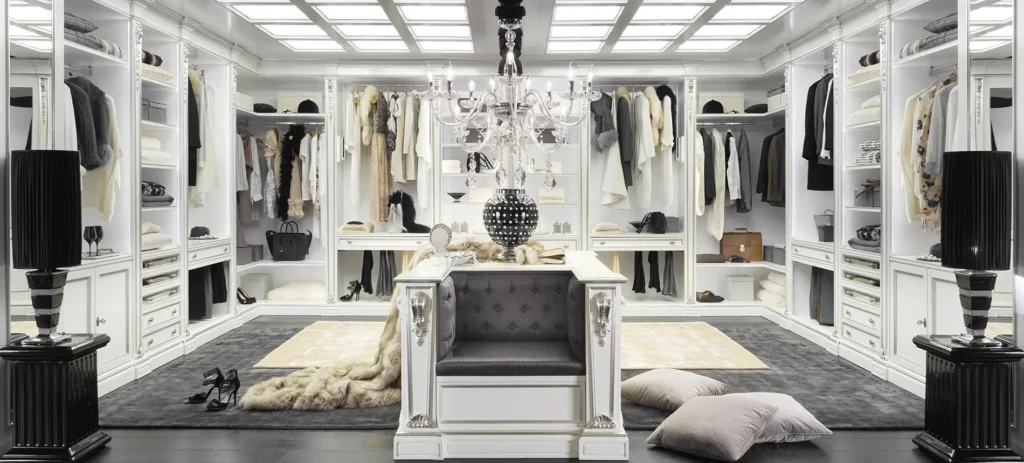
The Foundation: Selecting Nature’s Finest Materials
The journey of creating luxury Italian furniture begins long before any tool touches wood. Master craftsmen understand that exceptional pieces require exceptional materials. The selection process involves rigorous standards that have been refined over centuries:
- Wood moisture content must fall between 8-12% for optimal stability
- Grain patterns must show consistent character and aesthetic appeal
- Timber must be aged for a minimum of 3-5 years before use
- Each piece must be free from knots and imperfections that could compromise structural integrity
Traditional Italian furniture makers predominantly work with select hardwoods, each chosen for specific applications:
Wood Type | Primary Uses | Characteristics |
---|---|---|
Walnut | Cabinets, Tables | Rich color, excellent stability |
Cherry | Chairs, Decorative Elements | Fine grain, takes finish well |
Oak | Structural Components | Exceptional durability, prominent grain |
Maple | Inlay Work | Tight grain, resistant to wear |
The Masters Behind the Craft
Italian furniture artisans typically undergo 10-15 years of apprenticeship before being considered master craftsmen. This extensive training period ensures the preservation of traditional techniques while allowing for the integration of modern innovations. According to recent industry statistics, only about 15% of apprentices complete the full journey to master status, highlighting the demanding nature of the profession.
Traditional Techniques in Modern Times
While modern technology has revolutionized many industries, traditional Italian furniture making remains remarkably unchanged in its core processes. Hand tools account for approximately 70% of the work in premium pieces, with artisans using many of the same techniques their predecessors employed centuries ago:
Hand-Carving Excellence
The art of hand-carving represents perhaps the most distinctive aspect of Italian craftsmanship. Master carvers spend an average of 120-180 hours on intricate pieces, using up to 30 different specialized chisels to achieve the desired effects. The process involves several stages:
- Initial roughing out of basic forms (20% of total time)
- Secondary shaping to establish main features (30% of total time)
- Detail carving for ornamental elements (35% of total time)
- Final refinement and texture work (15% of total time)
The Finishing Touch: A Science and an Art
The finishing process in Italian furniture making is as crucial as the construction itself. Traditional workshops employ a multi-stage finishing process that can take up to six weeks to complete:
The Traditional Finishing Process
Each piece undergoes a minimum of 15 distinct finishing steps, including:
- Initial sanding sequence (progressing through 6-8 grit levels)
- Application of natural sealers (typically 2-3 coats)
- Hand-rubbed oil applications (4-6 layers)
- Traditional wax finishing (multiple thin coats)
- Final burnishing and polishing
Quality Markers: Identifying Superior Craftsmanship
For discerning collectors and connoisseurs, certain indicators distinguish truly exceptional pieces from mere replicas. Expert evaluators look for several key quality markers:
Construction Elements
Superior Italian furniture exhibits specific construction characteristics that indicate its authenticity and quality:
- Dovetail joints must be hand-cut with gaps no larger than 0.1mm
- Drawer bottoms should be solid wood, not less than 8mm thick
- Veneer, when used, must be at least 0.6mm thick (compared to 0.2-0.3mm in mass-produced furniture)
- All structural joints should incorporate traditional mechanical fastening methods
Preserving Heritage While Embracing Innovation
The Italian furniture-making tradition faces both challenges and opportunities in the modern era. While the industry has experienced a 15% decline in traditional apprenticeships over the past decade, there’s been a corresponding 25% increase in the value of handcrafted pieces, reflecting growing appreciation for authentic craftsmanship.
The Future of Traditional Craftsmanship
Contemporary Italian workshops are finding innovative ways to preserve their heritage while adapting to modern demands. Some notable developments include:
- Integration of 3D modeling for complex design visualization
- Development of natural, eco-friendly finishing techniques
- Implementation of humidity-controlled workshops for optimal wood stability
- Creation of digital archives documenting traditional techniques
A Legacy Written in Wood
The story of Italian furniture craftsmanship is one of enduring excellence, where each piece represents not just a functional object, but a testament to human creativity and dedication. As these traditions continue to evolve and adapt, they remain anchored in the timeless principles that have defined Italian excellence for centuries: uncompromising quality, artistic vision, and a deep respect for the materials and techniques that bring beauty into the world.
Today’s master craftsmen don’t simply preserve a tradition – they breathe new life into it with each piece they create, ensuring that the art of Italian furniture making continues to inspire and delight future generations. In a world increasingly dominated by mass production, these artisans remind us that true luxury lies not in quantity, but in the pursuit of perfection through patience, skill, and unwavering dedication to craft.